Practical Guide: Balancing Flail Mulchers & Forestry Mulchers
In this article, we explain the process of balancing mulcher rotors in a simple way. The goal is to extend the life of your machine, reduce noise and vibrations, and prevent premature wear.
The Underestimated Danger: Why Vibrations are Critical
Increased vibrations are often underestimated but can have serious consequences:
- Increased Wear: Bearings, gearboxes, and other rotating parts wear out faster, leading to frequent and expensive repairs.
- Bearing Damage: Defective bearings cause play, which amplifies the vibration. In the worst case, the bearing seats are damaged, requiring a costly workshop repair.
- Structural Damage: Cracks in the mulcher housing and leaks in the hydraulic system are common consequences.
- Loosened Screw Connections: Constant vibrations loosen bolts, which can lead to dangerous emergency situations.
- Downtime: Ultimately, this leads to unplanned machine failures in the middle of the season when it is most needed.
Why the "Old Method" Fails with Mulchers
We often hear: "I balance the rotor myself, put it on knife-edges and weld a weight on top until it stops turning." This method works for static unbalance on narrow discs. However, a mulcher rotor is long. Here, a heavy spot on one side can be balanced by a heavy spot on the opposite side. At a standstill, everything is in balance. But as soon as the rotor spins, the centrifugal forces pull these points in opposite directions, creating strong vibrations. This is called dynamic unbalance.
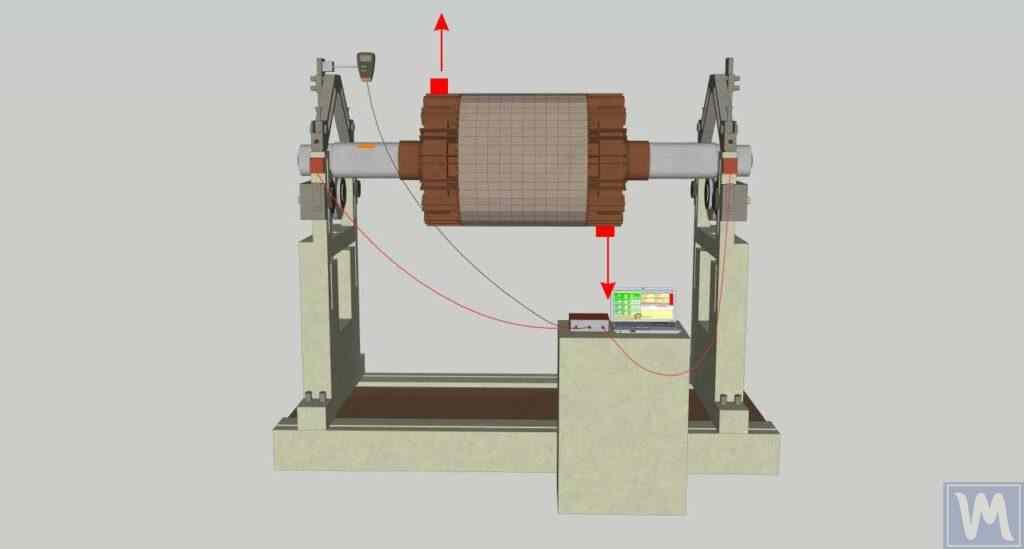
Dynamic unbalance can only be corrected with special equipment like the Balanset-1A, which allows for precise measurement in two planes.
The Balancing Process in Action
Why Balancing Can Fail: Common Problems & Solutions
You did everything according to the instructions, but the vibration got worse? This is often due to three main reasons:
1. Mechanical Defects
- Damaged Bearings: Check bearings and bearing seats for wear and play.
- Bent Shaft: A bent shaft cannot be balanced and must be replaced.
- Loose Connections: Ensure all mounting points of the mulcher are tightened.
- Cracks in the Housing: Check the housing for structural damage.
- Foreign Objects in the Rotor: Sometimes sand or dirt can accumulate inside the rotor tube.
2. Incorrect Balancing Conditions
- Resonance: If the operating speed matches a resonance frequency of the machine, balancing is difficult. Try changing the speed.
- Unstable Speed: The speed must be constant for every measurement.
- Changes During the Process: Do not lift the machine or change the structure (e.g., by welding reinforcements) between measurement runs.
3. Device Operation Errors
- Incorrect Sensor Installation: The sensor must be firmly seated on a clean, flat surface.
- Displaced Tachometer: The position of the laser tachometer must not change during measurements.
- Incorrect Angle Calculation: The angle for the correction weight is ALWAYS measured in the direction of rotation from the position of the trial mass.
- Insufficient Trial Mass: The trial mass must be large enough to cause a significant change in vibration (at least 20%).
Conclusion
The dynamic balancing of mulcher rotors is a precise process. With the right procedure and an understanding of potential sources of error, you can significantly extend the life of your equipment and avoid costly repairs. It is a worthwhile investment.